Understanding Cotter Pins: A Comprehensive Guide
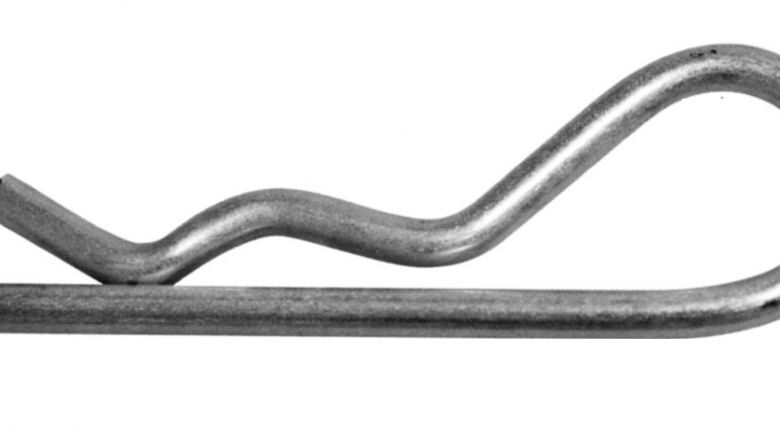
What is a Cotter Pin?
A cotter pin is a vital fastening device utilized in a variety of mechanical and engineering applications to secure two or more components together. Its primary purpose is to prevent the loosening of other fasteners, such as nuts and bolts, which can lead to mechanical failures. The structure of a cotter pin typically consists of a bent wire having two prongs that are inserted into a hole, with one end being pulled through and then bent inward to secure it in place. This simple yet effective design makes cotter. pins a commonly chosen solution in numerous industries.
Commonly crafted from materials such as stainless steel, brass, and carbon steel, cotter pins exhibit a range of mechanical properties that make them suitable for different environments. For instance, stainless steel cotter pins are often preferred in applications requiring corrosion resistance, such as in marine and automotive sectors. In contrast, carbon steel cotter .pins are renowned for their strength and durability, ideal for heavy-duty applications. The selection of material depends largely on the specific requirements of the application, including exposure to harsh conditions and the load-bearing capacity needed.
Cotter pins are available in various sizes and types, including split cotter pins, which feature a single split along the length for added flexibility and ease of installation. Another type is the solid cotter pin, which provides a more robust option suitable for applications with significant stress factors. By understanding the different types and their unique functionalities, professionals can make informed choices about which cotter. pin best meets their fastening needs. Ultimately, the cotter. pin serves an essential role in ensuring the integrity of mechanical connections, mitigating risks associated with loosening fasteners.
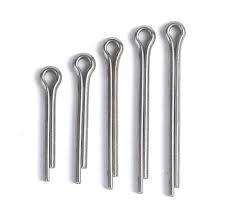
Applications of Cotter Pins
Cotter pins serve a vital function in numerous industries, acting as a simple yet effective fastening mechanism that ensures the integrity of various applications. Predominantly utilized in the automotive sector, cotter. pins are commonly found securing bolts on engine components, suspension systems, and wheels. Their role in automotive assemblies is to prevent loosening due to vibration and motion. The cotter. pin, by design, provides a reliable retention method, thereby guaranteeing the safety and functionality of vehicles.
In the realm of construction, cotter pins are equally indispensable. They are employed in securing scaffolding, anchoring structures, and even in heavy machinery such as cranes and excavators. The ease of installation and removal makes them an ideal choice for temporary setups, as they can be quickly inserted or pulled out without requiring specialized tools. This feature is particularly significant in construction environments where time efficiency and safety are critical.
Moreover, cotter. pins are not limited to automotive and construction applications. They are also prevalent in various machinery and equipment across industries such as agriculture, aviation, and manufacturing. For instance, in agricultural machinery, cotter pins are utilized to secure components on tractors and harvesters, ensuring smooth operation even under strenuous conditions. In aviation, these pins maintain the integrity of various aircraft systems, such as landing gear and control surfaces, where precision and reliability are paramount.
Case studies demonstrate the versatile nature of cotter. pins; many manufacturers have reported significant reductions in equipment failure rates due to the proper use of these fasteners. In summary, the applications of cotter pins span a wide array of industries, consistently providing reliable solutions for mechanical fastening and safety.
How to Properly Install and Remove Cotter Pins
Installing and removing cotter pins correctly is essential for maintaining the integrity of the components they secure. To begin with the installation process, one should first ensure that the hole in the assembly is properly aligned. This alignment facilitates the passage of the cotter. pin through the designated hole. When selecting a cotter pin, it is important to choose the appropriate size; a pin that is too large may not fit, while one that is too small may not provide adequate security.
Once the correct cotter .pin is chosen, insert the pin into the hole and allow the legs to extend outwards. At this stage, the next step is to bend the legs of the cotter. pin around the secured component to lock it in place. For optimal security, it is advisable to use pliers to bend the legs evenly, preventing potential damage to the cotter pin or the surrounding components. Additionally, ensuring that the legs of the pin are bent over sufficiently will help avoid any accidental dislodging during operation.
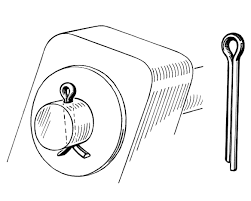
When it comes to removal, one should proceed carefully to prevent damaging any attached components. Start by removing any obstruction that may hinder access to the pin. Using a pair of pliers, grasp the bent legs of the cotter pin and gently twist them to straighten. It is crucial to apply steady pressure while ensuring not to break the pin in the process. Once the legs are straightened, the cotter. pin can be easily pulled from the hole. To enhance safety, always wear protective gloves during installation and removal, as metal pins can pose injury risks. Keeping these best practices in mind will ensure that cotter pins are both effectively installed and safely removed.
Choosing the Right Cotter Pin for Your Project
When selecting a cotter pin for your project, several critical factors must be considered to ensure optimal performance and reliability. Firstly, the size of the cotter pin is paramount. Cotter .pins come in various lengths and diameters, and the chosen size should correspond to the specific application requirements. A cotter. pin that is too small may not provide the necessary grip or security, while one that is too large can result in damage to the components being secured.
Next, the material of the cotter. pin plays a significant role in its suitability for different environments. Common materials include stainless steel, brass, and aluminum, each offering unique properties. Stainless steel cotter. pins are highly resistant to corrosion and are ideal for outdoor or industrial applications. Brass cotter pins, though less robust than stainless steel, provide excellent conductivity, making them suitable for electrical applications. Conversely, aluminum cotter pins are lightweight and suitable for applications where weight reduction is critical, such as in aerospace engineering.
It is also vital to consider the specific application type when choosing a cotter. pin. Different applications may have varying load requirements and environmental exposures. For instance, heavy-duty machinery may necessitate a stronger, more durable cotter pin, while light-duty uses may allow for more flexible options. Additionally, the installation process should not be overlooked; some projects may require cotter pins to be inserted in restricted spaces, prompting the need for pins with specific head designs or non-traditional configurations.
Finally, always consult industry standards and manufacturer guidelines to ensure compliance with safety regulations. By taking into account these factors—size, material, application type, and installation requirements—you can select the right cotter pin that will contribute to the efficacy and safety of your project.